In recent years, the mechanical equipment of cement enterprises, especially large equipment accidents frequently, causing serious losses to cement enterprises, therefore, cement enterprises in the production process of mechanical equipment repair and maintenance management, need to give the necessary attention to related issues and measures to ensure the effectiveness of mechanical equipment repair and maintenance management, which is conducive to prolonging the service life of machinery and equipment, and comprehensively improve the equipment repair and maintenance management level. Maintenance management level.
1 The necessity and importance of machinery and equipment maintenance
Maintenance of machinery and equipment is one of the core content of the daily management of enterprises, whether its performance is stable, safe, the production of product quality and cost will have a huge impact. Therefore, enterprises should strengthen the performance of various mechanical equipment maintenance efforts, so as to optimise the quality of enterprise products to provide protection, and ultimately reduce production costs.
Enterprises to do a good job in the maintenance of production equipment, is an effective form of stabilising the economic returns of enterprises. Specifically, to strengthen the enterprise in a variety of mechanical equipment maintenance work, not only can enhance product yield, optimise production efficiency, and can reduce consumption, cost savings, can help enterprises to maximize economic returns.
The premise and basis for the use of mechanical equipment is the daily use of equipment maintenance and repair. Equipment in the long-term, different environments in the use of the process, mechanical parts of the wear and tear, the gap increases, the use of performance changes, can directly affect the original design of the equipment balance. Equipment reliability, stability, use of benefits will be reduced, and even lead to the loss of mechanical equipment, its inherent basic performance, change the operating state caused by unnecessary accidents, enterprise production can not run normally. In the case of necessity for overhaul or replacement of new equipment, both increase the cost of enterprises, but also occupy the enterprise resource allocation.
Therefore, it is necessary to establish a scientific and effective management mechanism, increase the daily management and maintenance of equipment, scientific and reasonable development of equipment maintenance plan, and in each inspection and maintenance of the summary of the problems that occur, and further eliminate hidden dangers, improve the equipment management system for the efficient operation of the enterprise to provide protection.
2 The actual production of machinery and equipment inspection, repair and maintenance management process problems
2.1 Spare parts quality problems
In the cement machinery and equipment overhaul and maintenance management, found that the quality of spare parts have certain problems, the following chain hook and mill liner as an example.
Chain hooks of chain hoist were found to be worn fast and not durable due to defects in the material used to produce the chain hooks during the overhaul. The main problems in the design and manufacture of the chain hook are: (1) the load-bearing arc part of the chain hook does not use wear-resistant treatment, resulting in hard wear of the chain at the top of the sprocket wheel teeth, and frequent replacement of the chain hook after the wear increases, making it difficult for the hoist to work normally, and the implementation of the equipment overhaul and maintenance management work fails to achieve the expected results. (2) Chain hook material is too rigid, hardness increased, very easy to break, affecting the working performance of mechanical equipment, increasing the incidence of equipment failure, a serious threat to the safety of production.
The quality of the mill liner is the same problem that we should focus on. The liner is the most important key component of the mill, but also wear parts, need to be replaced regularly. In the design concept, the mill liner belongs to the casting parts, in addition to the length, width and height of the liner need to be processed in strict accordance with the drawings, the liner material needs to take into account the hardness and wear-resistant two needs.
In a mill liner replacement, consider increasing the wear resistance of the liner, its processing manufacturers to increase the wear resistance of the liner requirements, manufacturers in accordance with the requirements of the processing of a number of high degree of wear resistance of the liner. Replacement after the test, although the degree of wear resistance has been improved, but the hardness of the liner is greatly reduced, less than three months time, the mill liner one after another, the phenomenon of falling off, cracking. The reason for this is that the rigidity of the liner is far lower than the impact of the mill internal grinding body, can not withstand the continuous impact of the grinding body. No choice but to replace the liner again.
It can be seen that the quality of spare parts is crucial. There are countless manufacturers on the market, the material varies greatly, sometimes not only expensive is the best, the key is to meet their production needs, only the right is the best.
2.2 Inspection and maintenance process is not standardised
In order to achieve the long-term use of mechanical equipment failure in a timely and effective treatment, the need for equipment overhaul and maintenance management. However, part of the machinery and equipment due to overhaul process is not standardised, resulting in a decline in the efficiency of the equipment, invariably increasing the production costs of enterprises, specifically manifested as follows: (1) machinery and equipment overhaul of the existing overhaul process and the standard overhaul process of the equipment does not match the quality of the equipment overhaul is difficult to guarantee. For example, low-voltage motor bearing replacement process due to the lack of professional installation tools, in the new bearing installation, the use of hammer on the bearing for violent installation, installation process on the bearing inside, outside the jacket to exert external forces, resulting in bearing defects, service life is shortened for the accident to lay a hidden danger. (2) Some large-scale mechanical equipment in order to reduce costs, failed to carry out scientific assessment of the working performance of the equipment, resulting in the long-term use of the equipment potential safety hazards can not be eliminated in a timely manner, or potential hazards are not found. For example, cement mill hollow shaft flaw detection and cement mill cylinder flaw detection. (3) The lack of innovation in mechanical equipment overhaul, overhaul is only for the repair of damaged equipment, and the lack of systematic expansion of thinking. For example, why is the damaged part damaged? What is the cause? Will it be damaged again after replacement? These issues often do not attract attention, and some mechanical problems even occur many times. For the inspection and maintenance of the summary, just a simple form, only the cost of maintenance and a simple summary of the process, the lack of summary of the underlying causes, week after week, the formation of the phenomenon of maintenance simply for the maintenance of the maintenance of the phenomenon.
2.3 Inspection and maintenance process safety awareness is weak
Many companies from the cost point of view, not equipped with enough professional technicians and safety officers, and can not monitor the maintenance process in real time. Mechanical equipment inspection and maintenance process of poor safety awareness is mainly reflected in two aspects, one is the safety of equipment, the second is the safety of personnel.
Equipment safety is mainly manifested in: unprincipled replacement of spare parts, different models and specifications for the acute replacement of equipment for the later operation of hidden dangers; dismantling the process of violent dismantling, installation, to the mechanical equipment caused by man-made damages, increase costs.
Personnel safety is mainly manifested in: in the inspection and maintenance process due to the risk factors identification is incomplete, the lack of supervision, resulting in mechanical collision, fall, squeeze hand and other injuries, resulting in the enhancement of business costs, but also cause adverse social impact.
Therefore, it is necessary to strengthen the management of inspection and maintenance mission statement. Before inspection and maintenance, the task book should be filled in carefully and in detail, and the risk factors in the implementation process should be fully identified, and the level of identification of risk factors depends on the training in daily work and the training of the team leader. Only by giving full play to the supervisory role of the team leader and ensuring the truthfulness and effectiveness of the inspection and maintenance task book can the safety of personnel and equipment be guaranteed to the maximum extent.
3 Improvement measures in the process of mechanical equipment maintenance
3.1 Daily inspection of equipment
Lack of necessary system constraints, or have a system constraints but in vain, or lack of equipment should be professional knowledge, these will cause in the daily inspection do not know what to check. Equipment maintenance work should be strictly in accordance with the relevant provisions of the daily inspection of all kinds of machinery and equipment in detail, to accurately understand whether there are faults or factors that may cause failure.
In the process of daily inspection, equipment maintenance workers can not only use their senses to make intuitive judgement on the operation of machinery and equipment, but also with the help of professional instruments, such as handheld vibration meter, infrared temperature gun to carry out a comprehensive inspection of machinery and equipment. Through the accumulation of data, identify changes in equipment parameters, thereby improving the predictability of accidents. At the same time, it is also necessary for the staff to have rich experience in daily inspection.
3.2 Grasp the key links of daily inspection
Mechanical equipment maintenance staff in the daily maintenance work, the author from their own work experience, that should focus on the following five aspects of the content: First, to see whether the mechanical equipment oil leakage phenomenon; Second, to see the mechanical equipment in the transmission parts or connecting parts of the wear and tear traces of iron powder, if there is a problem should be as soon as possible to find out the reasons for and repair in a timely manner; Third is to see all the load-bearing, pressure-bearing parts of the Whether there is a problem of loosening of the various bolts, if there is off or loose should be filled or reinforced as soon as possible; four is to view all the lubrication of the position of the lubrication of the machine parts is normal, if there is a problem should be dealt with as soon as possible; five is to listen to the equipment to determine whether there is anomalous sound, if there is a different response to find out the source of the noise as soon as possible.
In short, equipment maintenance workers should be combined with the specific structure of machinery and equipment to carry out targeted inspection, focusing on load-bearing force and transmission parts, in order to ensure the timely discovery of equipment problems.
3.3 Strengthen the learning and application of new technologies for mechanical equipment.
With the cement enterprises on mechanical equipment performance requirements and daily inspection and maintenance of the quality of work required to further increase the quality of mechanical equipment to enhance their own operation, technology and equipment need to be constantly updated, professional and technical personnel to keep pace with the learning of new technologies to keep up with the rapid development of social needs.
Usually, part of the hoist and belt drive part of the cement enterprise, a large number of use of ZQ reducer, the operation cycle is too long, most of the oil leakage phenomenon, governance is very difficult, not only increase the cost of the enterprise, but also increase the environmental protection hidden danger. With the continuous improvement of permanent magnet motor technology, the use of permanent magnet motors instead of ZQ reducer transmission, is not an effective way. Permanent magnet motor has a large starting torque, easy to adjust the speed, efficiency and other advantages, and eliminates the deceleration of this link, the performance can completely replace the ZQ reducer, and later maintenance is greatly reduced.
3.4 Establish a sound mechanical equipment inspection and maintenance management system
Enterprises want to do a good job of maintenance of machinery and equipment, need to build a sound management system according to their own specific circumstances, in order to provide a reliable basis for the daily operation of equipment maintenance, and ultimately significantly improve the maintenance process specification and the effect of the ideal; and also need a set of normal operation of the supervision system, to ensure that the system can be a strong implementation.
In the process of developing a sound mechanical equipment maintenance system, enterprises should do the following two points: First, sound mechanical equipment management organisation. With the implementation of the form of responsibility of the management workers to improve the maintenance of mechanical equipment. For example, the formation of special machinery and equipment maintenance team, the team leader of a variety of mechanical equipment maintenance work for the overall management of the daily work of various equipment maintenance workers and the effect of strict inspection. Secondly, the construction of sound mechanical equipment maintenance standards, choose the most suitable maintenance strategy. For example, for the type of mechanical equipment failure targeted design maintenance methods, the need for overhaul, then, should do a good job of all the preparatory work, according to the overhaul of technical standards for the implementation of scientific maintenance.
In the process of maintenance of machinery and equipment, should be in the form of a system to ensure a clear division of responsibility, whether it is inspection, maintenance or use, need to be combined with the provisions of the provisions of the orderly manner. After each overhaul, but also seriously do a good job of summarising and analysing, and strengthen the focus of the later maintenance.
Conclusion
The rapid development of modern cement enterprises, in China’s national economic development process plays an important role in safeguarding. Cement production process to carry out mechanical equipment overhaul and maintenance management at the same time, the need to strengthen the problem of the measures to give mechanical equipment performance? The necessary safety guarantee, and optimise the long-term use of mechanical equipment repair and maintenance management, to promote the modern cement enterprises can maintain good production efficiency and social benefits.
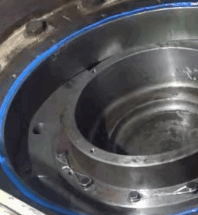