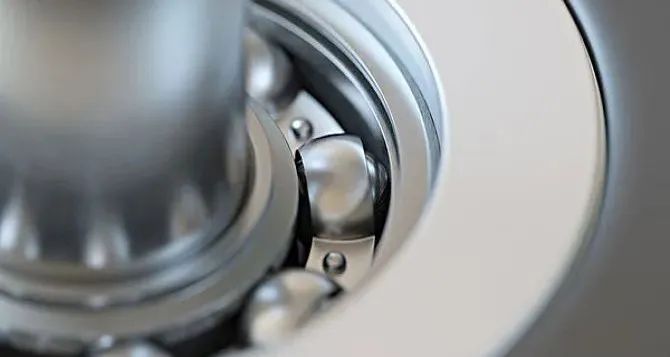
In the mounting of bearings there are cleaning, drying, (grease encapsulation) test runs, etc., which should be carried out on the basis of observing all precautions.
When using precision rolling bearings, the mounting of the bearings is very important in order to obtain the highest speed and a low temperature rise.
Step 1: Clean the bearings and remove the anti-rust oil
After soaking in a highly volatile solvent such as refined paraffin and naphthol and cleaning by hand rotation, remove refined paraffin etc. with petrol or ethanol. When blowing off the cleaning oil with an air gun, attention should be paid to the cleanliness of the air.
When using the oil and air lubrication method, it can be used directly, but it is recommended to apply or soak in lubricating oil or low viscosity oil after cleaning.
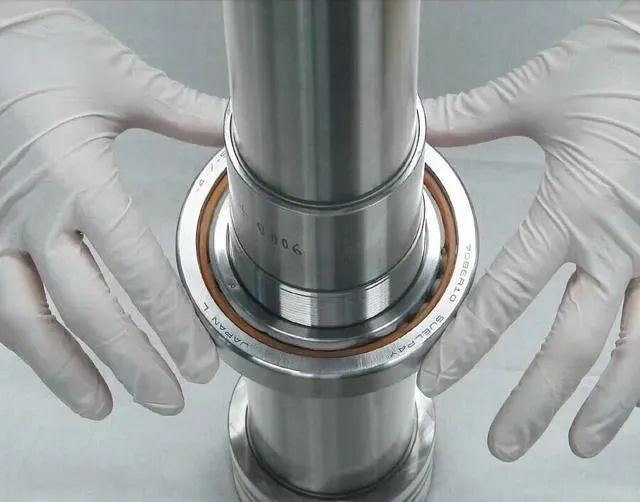
Step 2: Dry the bearings without moisture residue
When using grease lubrication, the bearings need to be sufficiently dry in order to prevent the grease from running out.
In addition, the grease should be sealed in immediately after drying. Drying can be carried out in warm air (care needs to be taken with the cleanliness of the air) or in a constant temperature bath.
Step 3: Grease encapsulation
After encapsulation, the rolling part is rotated by hand so that the grease is well coated.
Ball bearings can be used with a syringe, vinyl bag aligned with the inner ring rolling surface, between the ball and the ball equal amount of encapsulated grease. When there is a raceway ring guide cage, it is recommended to use a small tool such as a spatula to apply to the cage guide surface. If it is not possible to seal the rolling surface of the inner ring due to the narrow space in the inner ring, seal the rolling surface of the outer ring. In this case, every effort should be made to make the grease penetrate into the inner ring by hand rotation.
When applying grease to the outer diameter surface (inner diameter surface) of the roller bearing, use your fingertips to turn the roller so that the grease penetrates into the inner ring (outer ring).
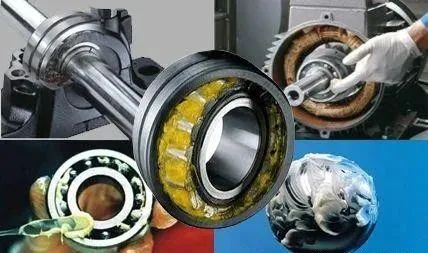
Step 4: Test run
1、Oil and air, oil mist lubrication
In oil lubrication, the bearing temperature reaches a steady state in a relatively short period of time before reaching its peak, therefore, test running is relatively simple. It is recommended to keep at 2000-3000 rpm for about 30 minutes and gradually increase to working speed. However, dmn (rolling body centre diameter * speed) more than 1 million times the range, in order to ensure safety, should be 1000-2000 revolutions per minute for speed.
2、Grease lubrication
In grease lubrication, in order to make the temperature rise stable, test run is very important. Test run, the speed increases, showing that the temperature rises faster, after reaching the peak, the temperature will be slow and stable. Need a certain amount of time to reach stability.
3、Ball bearings
It is recommended to use 1000-2000 revolutions per minute as a unit, and then speed up after the temperature has stabilised. dmn (rolling body centre diameter*speed) exceeds 400,000 times, for safety reasons, 500-1000 revolutions per minute should be used as a unit to speed up.
4、Roller bearings
Compared with ball bearings, the peak temperature and the time to reach a stable temperature are longer for roller bearings during test runs. In addition, the temperature change cannot be stabilised due to the temperature rise caused by the re-rolling of grease, so they should be run at maximum speed for a longer period of time. It is advisable to run the bearing at 500-1000 revolutions per minute until the temperature has stabilised. dmn (rolling element centre diameter*speed) exceeds 300,000 revolutions, so for safety reasons it should be run at 300 revolutions.
Step 5: Assembling the bearings
When assembling bearings on spindles, the inner ring of the shaft and bearing is an interference fit (tight fit) and is usually assembled by pressing in with a hydraulic press or by hot fitting.
Whichever method is used, it is necessary to reduce the impact of the assembly and maintain the accuracy of the bearing.
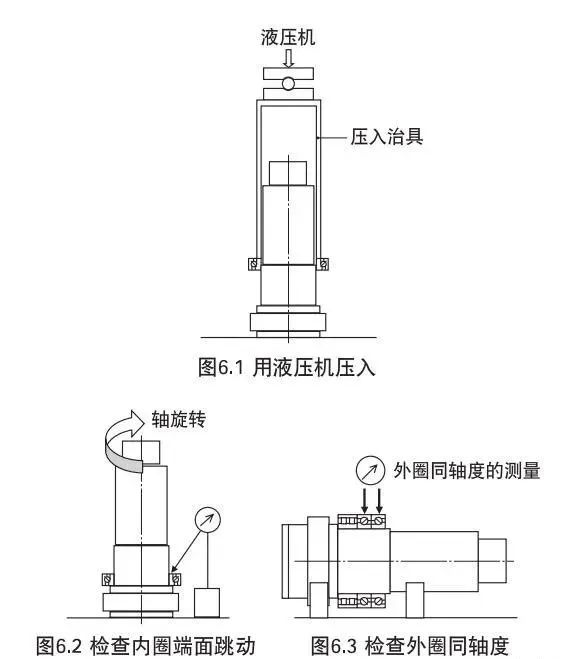
1、Pressing in with a hydraulic press
When pressing in bearings by means of a manual press etc., it is first necessary to calculate the press-in force generated by the interference between the shaft and the inner ring (a hydraulic press with a working pressure greater than the required pressure must be used).
Then, when pressing in the inner ring, use the inner ring press-in tool and press it firmly into the shaft shoulder (do not apply force to the outer ring). After pressing in, measure the accuracy of each part of the bearing to confirm that it is actually mounted on the shaft. In addition, when assembling a multi-row bearing, the runout should be measured after assembly to correct the shaft centre deviation between the outer rings.
2、Insert by hot mounting
Make full use of thermal expansion and contraction, heat expansion and inserted into the bearing, generally is heated to the extent of 30 degrees, need to pay attention to: the use of resin materials as the cage of angular contact ball bearings, do not heat to too high a temperature, the highest shall not be higher than 80 degrees. And because of cooling, the inner ring shrinks towards the shaft, the bearing – shoulder between the clearance will be generated, therefore, after the fit down to room temperature, and then pressed with hydraulic press, etc..
Also check the verticality after cooling. When heating with a bearing heater, be careful of excessive temperature rise and use equipment with a demagnetising device that can remove residual magnetism.
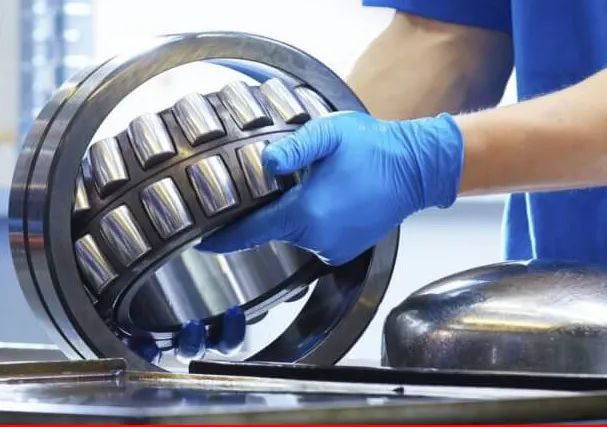
Step 6: Fixing the inner ring
When mounting and securing bearings on spindles, the bearings are usually tightened with a trapezoidal socket or precision bearing nut on the inner ring side and a bolt on the outer ring side to fasten the front cover. When using a trapezoidal sleeve or precision bearing nut to tighten the inner ring, the following points should be noted.
1、Fixing with trapezoidal sleeve
Trapezoidal sleeve will be oil pressure and expansion of the sleeve into the shaft, apply the required pressure into the force (tightening force), remove the oil pressure, in the sleeve fixed on the shaft at the same time to the bearing to apply the lyrical tightening force, is a relatively easy fixing method.
However, as the sleeve is held in place only by interference with the shaft, it may loosen when the shaft is bent and subjected to moment loads.
Therefore, in most cases the fixing method with the bearing nut shown in the figure below is used.
2、Tightening with a precision bearing nut
Precision bearing nuts (precision locknuts) are tightened with the appropriate tightening force in accordance with the tightening torque regulations for precision locknuts.
In addition, when the bearing is fixed with a precision bearing nut, the nut is tilted due to the play in the threaded part, and may need to be fine-tuned in order to achieve shaft rotation accuracy.
- Relationship between tightening torque and tightening force of precision bearing nuts
As the threaded surface of the precision bearing nut and the threaded surface of the shaft and the seating surface of the precision bearing nut are sliding surfaces, the relationship between the torque and the tightening force will change according to the friction coefficient when tightening, and should be adequately ground.
It is also important to calibrate (calibrate) the relationship between tightening torque and tightening force using force measuring washers etc. in advance.
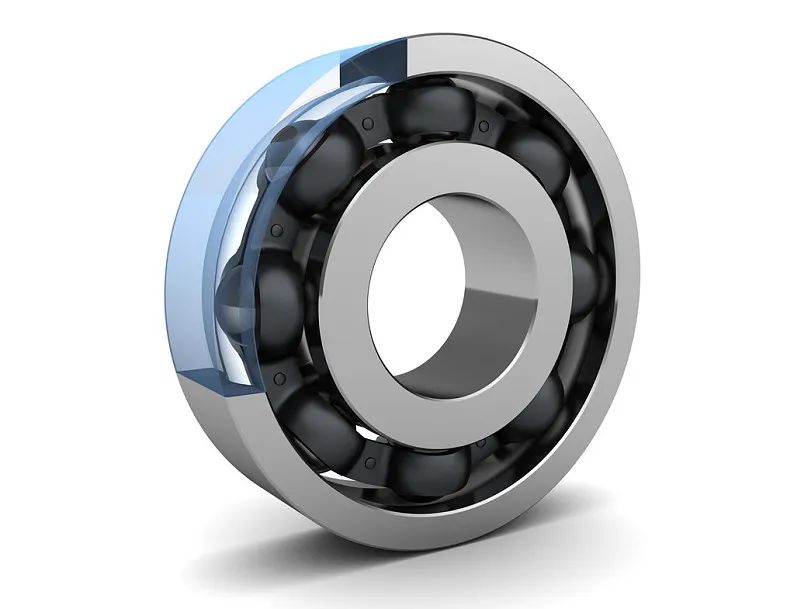
By now, the installation of bearings has been basically completed, in the process of installation, we should also pay attention to the problems that may lead to such as gasket deformation, front cover crimping to produce margin, clearance is too large or too small, etc., to ensure that the installed bearings can maintain the best operating condition, long time operation without failure.