Abstract: Rolling bearings mainly play the role of supporting transmission components in the aviation industry, and are in a high-load, high-speed working environment. Through the research on the use of rolling bearings, the cause of failure is analyzed, and it is pointed out that the rolling bearings are guaranteed to be evenly loaded during use, the bearings are assembled according to process requirements, reliable lubrication and sealing methods are adopted, and measures to prevent failures can be effectively extended. Provide strong technical support to ensure aviation safety.
0 Preface
Aeronautical rolling bearings require high precision, complex operating environments and harsh operating conditions. They are mainly used in engines, motors, pump bodies and control systems, and their quality directly affects the reliability of aircraft systems. Due to its own quality and external conditions during use, the bearing loses its original design function, resulting in failure or failure to work normally, which is called failure. In actual work and use, if the installation and adjustment standards are not high, there are collision damage, poor lubrication and maintenance, and hidden troubles are not eliminated in time, leading to premature damage and destruction of the bearing, which is called early failure. By collecting a large amount of data of early failure bearings, conducting exploration and research, finding out the cause of failure, and proposing preventive measures, effectively improving the service life and reliability of bearings.
1 The form of rolling bearing failure
The failure states of rolling bearings can be divided into two types: non-stop failure and deadlift failure. Stall failure means that the bearing has an unexpected situation and stops rotating due to loss of working ability, such as cracks, jamming, etc. Insufficiency failure means that the basic size and surface accuracy of the part change during use, and the fit clearance exceeds the original design standard. Although it can continue to rotate, it is abnormal operation, such as wear, burns, corrosion, etc. There are mainly eight types of failures.
1.1 Wear failure
Wear occurs when the rolling elements and raceways of rolling bearings move relative to each other. When dirt, sand, or flaked iron filings enter the lubricant, it prevents the formation of an oil film on the raceway surface and aggravates wear. Continued wear causes the bearing not to work properly, known as bearing wear failure.
1.2 Fatigue pitting failure
The rolling elements of the rolling bearing and the inner and outer rings are constantly rotating, and the contact surface is repeatedly affected by the pulsating load, causing fatigue cracks at a certain depth under the surface, forming fatigue pitting, and causing the bearing to fail to rotate normally.
1.3 Corrosion failure
The surface of each metal part of the bearing undergoes chemical or electrochemical reaction with the environmental medium, and the surface damage and failure caused by it are called corrosion failure. The manifestation is rust or chemical corrosion.
1.4 Plastic deformation failure
When the bearing speed is very low (n<10 r/min) or swings intermittently, under the action of a large impact load or static load, the local stress of the bearing raceway and the contact point of the rolling element will exceed the yield limit of the material, resulting in plastic deformation. Continuous rotation leads to failure of bearing plastic deformation.
1.5 Peeling failure
The contact surfaces of rolling elements and raceways that bear relatively large loads and relatively move, due to repeated loads, the metal surface layer peels off in flakes, resulting in peeling failure.
1.6 Fracture failure
Breakage of bearing parts will cause sudden failure accidents. Due to improper assembly, use and maintenance, poor lubrication and sealing, and debris entering, the components of the bearing are broken and broken, causing the bearing to break and fail.
1.7 Galvanic corrosion failure
Due to the limitation of repair methods, when welding is required on aircraft equipment, the welding current passes through the bearings installed on the equipment, causing damage to the bearing surface and causing electric corrosion failure.
1.8 Burn failure
The raceway or rolling element surface of the inner and outer rings of the bearing and the cage are in rotation, due to rapid heating until discoloration, softening, welding and damage, it is called burn failure. When under load, factors such as poor lubrication, poor quality lubricating oil, foreign matter mixed with lubricating oil, incorrect assembly and other factors cause the temperature to be higher than the design value, burn the bearing, and cause tempering of the bearing raceway and rolling elements.
2 Reasons for failure of rolling bearings
According to big data statistics, the main factors causing early failure of bearings are as follows: overloading accounts for 9%, insufficient lubrication accounts for 32%, pollutants account for 16%, installation and commissioning accounts for 13%, and improper maintenance accounts for 22%. , others accounted for 8%.
2.1 Failure analysis caused by improper lubrication and sealing
Lubrication and sealing have an important impact on the service life and operating vibration of rolling bearings. Correct use of lubricants and research to improve sealing performance are crucial to the reliability and service life of bearings. If there is a problem, it will easily cause surface gluing, wear, Corrosion, cavitation, burns and other failures.
(1) The product expires. If the expired and deteriorated lubricant containing impurities is used for lubrication, the friction coefficient between the bearing rolling body and the contact surface of the inner and outer rings will be increased, so that the bearing will fail early.
(2) The model is wrong. The type of lubricant is incorrect or the quality is poor, which will fail to achieve the purpose of lubrication and accelerate the failure of the bearing.
(3) The amount of injection is small. If the amount of lubricant injected is too small, the lubrication effect is insufficient, resulting in dry friction and heat generation, thereby accelerating the fatigue pitting and wear of the bearing, and causing the bearing to fail.
(4) Loss and deterioration. Instruments? The equipment has been sealed for a long time and parked unused, resulting in loss of lubricant or solidification and deterioration. When the equipment and instruments are restarted, the lubricant is not updated, which accelerates the failure of the bearing.
(5) Wrong seal. The sealing form of rolling bearing is unreasonable, and the construction method is incorrect: pollutants such as silt, sand, water, and chemical agents invade the inside of the bearing, which aggravates wear during operation; due to the loss of lubricant, the lubrication effect is lost.
2.2 Failure analysis caused by improper installation
If the installation method and means are incorrect, the installation accuracy will not be achieved, and the bearing will run in an abnormal state? The original accuracy, life and performance of the bearing will be greatly reduced, resulting in early failure. Most bearing failure modes are directly related to installation.
(1) The assembly is not standard. If the bearing assembly is not carried out according to the process requirements and technical standards, the bearing parts will be damaged, deformed, and the coaxiality will be out of tolerance, vibration and wear will occur during operation, which will reduce the performance and shorten the service life.
(2) Large assembly clearance. If the clearance is too large during bearing assembly, the rolling elements will vibrate greatly, which will aggravate the impact of the rolling elements and the inner and outer ring raceways, resulting in plastic deformation or even permanent deformation, which will accelerate the early failure of the bearing.
(3) The assembly clearance is small. When the bearing is assembled, if the clearance is too small, it will cause friction between the rolling elements and the raceways of the inner and outer rings, resulting in increased wear, increased temperature, and prone to burns and seizures.
(4) The fit clearance is large. During the assembly process, the matching clearance between the inner ring of the bearing and the transmission shaft, and the outer ring and the bearing seat hole is too large, which reduces the assembly accuracy, is prone to rotation crawling, aggravates the wear of the mating surface, and reduces the rotation accuracy.
(5) The fit clearance is small. During the assembly process, the matching clearance between the inner ring of the bearing and the drive shaft, and the outer ring and the bearing seat hole is too small. If the assembly is carried out by force, the inner and outer rings are easily deformed, or even cracked or broken, resulting in failure of the bearing.
2.3 Failure analysis caused by improper maintenance
Adhering to daily maintenance and regular maintenance is an important means to prolong the service life of bearings, otherwise it is easy to cause failure forms such as abrasive wear, corrosion, plastic deformation of bearings, and shorten the service life of bearings.
(1) Use of grease. The way of using grease lubrication without maintenance and inspection for a long time will easily damage the sealing form and cause the loss of grease. If the required grease cannot be added in time, dry friction will be formed; secondly, it is easy to enter dust, sundries, compounds, Accelerate the wear of the bearing and cause early failure.
(2) Use of lubricating oil. Using lubricating oil lubrication, without maintenance and inspection for a long time, the sealed container is defective, the lubricating oil leaks, the oil scraper ring, oil pump, etc. cannot supply oil to the bearing, forming dry friction, resulting in early failure of the bearing.
(3) The influence of external force load. The bearing is affected by the load and external force, and loses the standard of the original equipment during the movement process. If it is not maintained and corrected in time, and it is operated in an abnormal state for a long time, it is easy to cause early failure of the bearing.
3 Prevention of rolling bearing failure
In the aviation field, rolling bearings replace wearing parts according to the use environment, standards and service life. However, through the investigation and analysis of big data, many bearings did not reach the expected service life when they failed. Therefore, formulate the following effective measures to prolong the service life of bearings and prevent early failure.
3.1 Strictly control the product quality of rolling bearings
The quality gate should be moved forward, and the tracking supervision and quality inspection of the bearing production process should be increased to ensure that the indicators of the finished product meet the design requirements. Strict tracking supervision and quality inspection are important means to prevent early bearing failure. When assembling and using, unseal the bearing correctly according to the requirements, clean the lubricant when it is sealed, and add new lubricant; visually inspect the rolling elements for pitting and discoloration, and whether the inner and outer rings are worn or corroded. Whether the frame is twisted or broken. Resolutely put an end to the installation and use of unqualified products.
3.2 Improve the installation quality of rolling bearings
The difference in the life of the bearing depends not only on the material and manufacturing accuracy, but also on the assembly process. During the bearing assembly process, the corresponding assembly method should be adopted according to the bearing structure, characteristics, dimensional accuracy, and matching accuracy. Improper assembly may cause damage to the parts of the bearing and affect the performance and life of the bearing.
3.3 Keep the rolling bearings well lubricated
The quality of lubrication is directly related to whether the rolling bearing can operate normally, and plays a decisive role in many factors such as bearing sealing, anti-corrosion, wear, heat dissipation, and shock mitigation. If rolling bearings are used in poor working environment and harsh conditions, affected by alternating loads and impact loads, if unqualified lubricating oil and unqualified lubricating grease are used, it will have a great negative impact on the operation of the bearing. Therefore, correct selection of the type and grade of lubricant, adoption of scientific lubrication methods, strict implementation of lubrication operating procedures, and maintenance of good lubrication effect and lubrication state are effective measures to reduce the failure of rolling bearings such as wear, corrosion, and gluing.
3.4 Do a good job in the maintenance of rolling bearings
Adopt a reasonable bearing sealing form, maintain a good sealing state, prevent the loss of lubricant during operation, and prevent the intrusion of sand, dust, sundries, water, chemical agents and other pollutants, so as not to reduce the lubrication effect and aggravate the wear of the bearing. In daily maintenance, do a good job of cleaning to prevent pollutants from entering the interior of the bearing as much as possible. If it is found that the bearing lubricant is lost or contaminated, it should be cleaned immediately, refill the clean lubricant, and improve the sealing conditions to ensure reliable sealing.
3.5 Monitoring the effective operation of rolling bearings
Predicting and diagnosing bearings in operation is an important means to improve bearing reliability and service life. Bearing prediction and diagnosis technology is associated with high-precision testing systems and detection methods. Vibration meters, digital thermometers, stethoscopes and other simple instruments can help maintenance personnel detect faulty bearings, using various types of fault monitoring The multi-parameter monitoring of the instrument is very effective for accurately detecting hidden fault points. Predict and diagnose the running state of the bearing as early as possible through advanced instruments and methods, and take effective measures to improve the reliability and service life of the bearing.
4 Conclusion
In the process of rolling bearing failure analysis, through the collection of failure big data, repeated exploration and research to obtain correct data and results, find the real reason, take effective measures to improve performance, prolong service life, and ensure the reliability of bearing operation. Ensure aviation safety assistance.
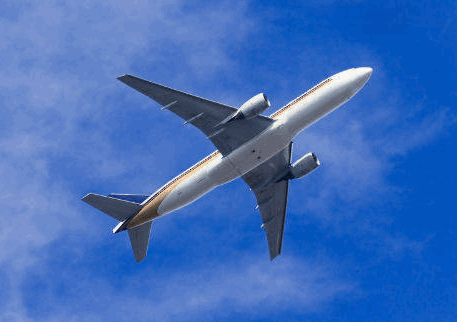