A major breakthrough was achieved for the ultra-large runner centre body forgings of single-engine capacity 500MW-class high-head, large-capacity impact hydraulic turbine
The ultra-large runner center body forgings of single-engine capacity 500MW high-head large-capacity impact hydraulic turbine developed by SINOMACH successfully passed the ultrasonic flaw inspection before tempering. This marks a major breakthrough in the field of ultra-large martensitic stainless steel forgings for hydropower in the Group’s engineering application of steel purification smelting, profiling forging of thick and large pie-shaped parts and coordinated control of forging process organization and shape.
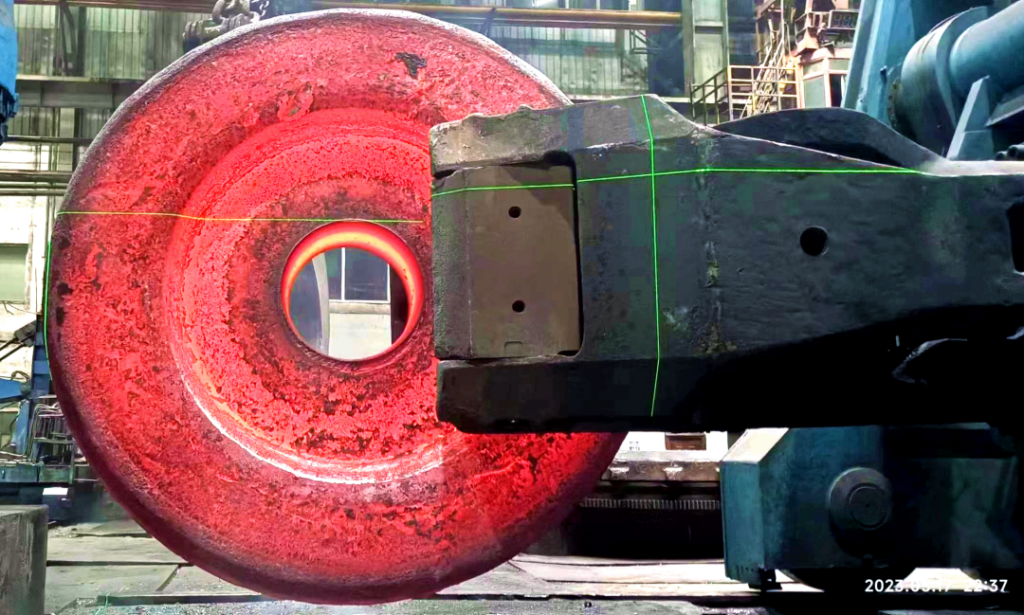
The forging is a key core component of high head, large capacity impact turbine, which is jointly developed by Erzhong (Deyang) Heavy Equipment Co. -Zala Hydropower Station. Zala Hydropower Station is the core power station of the clean energy integration base in southeast Tibet, and is the only hydropower project in China that can carry out the development and application demonstration of 500MW high head large capacity impact type unit, which is of great significance to the realization of national energy security and “Tibetan power outward” energy development strategy.
Through systematic research on basic material characteristics and manufacturing process technology, the company has made continuous breakthroughs in forging smelting, forging and flaw detection to help the construction of major clean energy projects.
World’s advanced heavy-duty gas turbine core castings successfully developed
The last set of M701J type gas turbine developed by SINOMACH passed the joint inspection and was sent to the customer site. Thus, all 8 sets of products developed by the Group were delivered, becoming the first enterprise in China to successfully master the manufacturing technology of high-end heavy-duty combustion turbine castings covering all levels of E, F and H/J classes and achieve mass production.
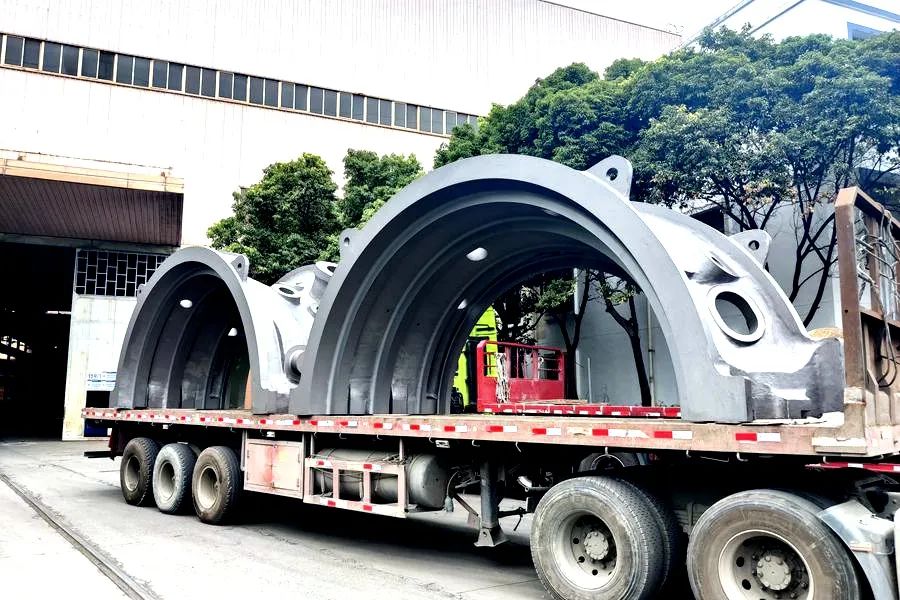
The castings are developed by Ershong Equipment, making full use of numerical simulation technology and lean management tools to carry out multifield coupling simulation calculations of filling, solidification and stress and value stream analysis of the whole process, and overcome key manufacturing technologies such as thin-walled complex cast steel parts for high quality H/J class heavy-duty combustion engines, providing important support for the localization of China’s heavy-duty combustion engines and safeguarding China’s energy security.
China’s first non-wood continuous press production line successfully rolls off the production line
A non-wood continuous press production line developed by SINOMACH has successfully rolled off the production line, which is the first production line in China to use the continuous flat press method to press PVC plastic or rubber granules into rolled panels.
The production line was developed by Suzhou Sufma Machinery Co., Ltd, a subsidiary of the Group. Unlike the existing roll press production method in China, this production line plastic granule raw material plasticising process combined with continuous flat press hot pressing technology breaks the original speed bottleneck and better solves the problems such as low production efficiency in the field of PVC plastic or rubber coil board manufacturing, realising the application of continuous flat press in the plastic flooring industry.
Successful commissioning of excitation equipment for “gas-to-coal” cogeneration project
The excitation equipment of the 2×460MW “gas-to-coal” cogeneration project developed by SINOMACH has completed all tests and was successfully put into operation, which will contribute to the achievement of the “double carbon” target in the Guangzhou Development Zone.
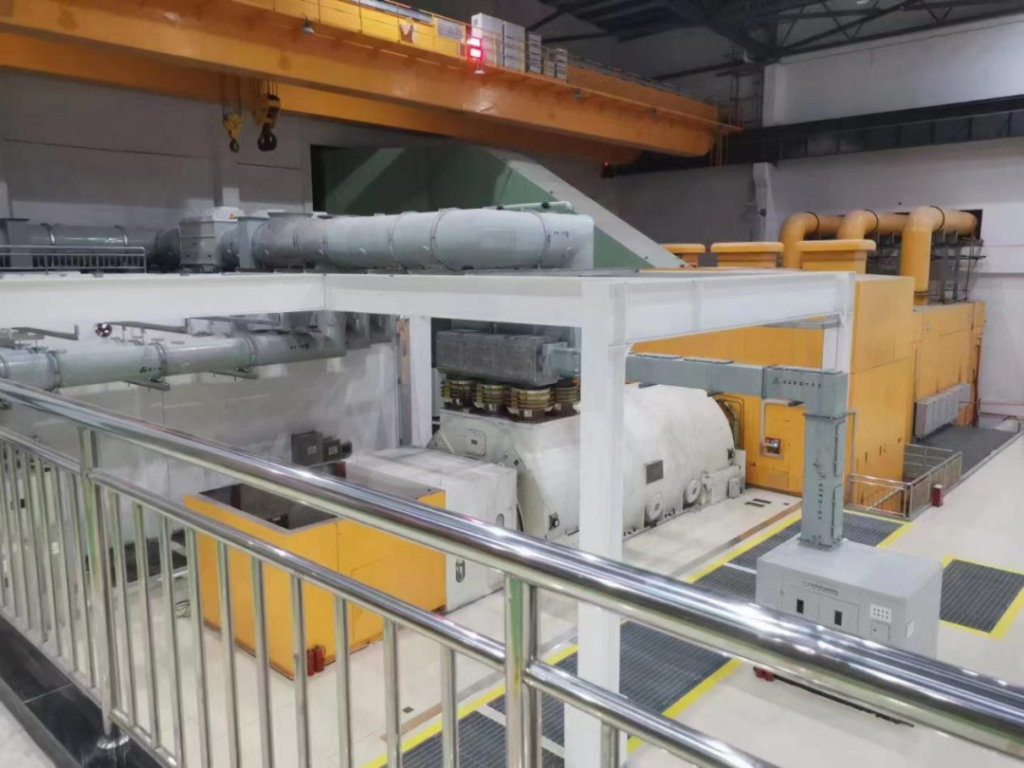
The 2 x 460MW “Gas to Coal” Cogeneration Project is a key project in Guangdong Province, Guangzhou City and Huangpu District, and its excitation system is developed by Guangzhou Prime Industries Limited, a subsidiary of the Group. The unit is an improved gas-steam combined cycle cogeneration unit (F-class improved), which uses natural gas as fuel and provides energy in the form of cooling, heating and power triple-supply. Upon commissioning, the unit will generate 4,500 hours of power annually and will support the regional power grid in the centre of Guangzhou.