The spooler is a key piece of equipment in the high-speed wire rod production line and is located between the water-cooled section and the bulk coil transporter after the finishing mill. At high speeds, the spooler can reach 110-160m/s and the temperature at its exit can be over 600°C. Under high speed and high temperature conditions, the spinner will inevitably suffer from mechanical problems. Some of the more common mechanical problems include excessive vibration, wear and tear of the spinning discs and bearing failure, all of which have an impact on the normal operation of the spinning machine and the quality of the coil. By implementing reasonable optimisation measures, mechanical vibration and wear can be reduced to a certain extent, thus reducing the probability of equipment failure.
1 Analysis of the working principle of the spooler and the spooling process
1.1 The working principle of the spooler
The wire spitting machine is one of the core equipment of the high wire production line and is mainly used for the production of coils of various diameters. Hand Steel high-speed wire production line introduced the British ASHLOW spitting machine, the spitting machine for the horizontal structure, the diameter of 1075mm, the horizontal angle of 20 °, and with the head positioning and vibration function, to ensure the quality of the coil spiral, can be adjusted to set the length of the coil, to facilitate the collection of coil products, bundling. The spooling machine is mainly composed of the motor, spooling disc, spooling tube, transmission device, hollow shaft and bearing seat. The basic working principle of the spitting machine is to use the centrifugal force of the high-speed rotation to reprocess the wire rolled by the finishing mill into a continuous coil of a certain diameter. The hollow shaft of the spooling machine is driven by the electric motor and speed increaser to rotate at high speed. The wire rolled by the high-speed finishing mill is sent through the ducts and pinch rollers to the hollow shaft of the spooling machine, where the high-speed rotation of the hollow shaft simultaneously drives the spooling discs and tubes fixed to the hollow shaft to rotate at high speed. The wire entering the hollow shaft is spit out along the circumferential tangent of the hollow shaft by the centrifugal force of the rotating disc and tube, and the spitted coils are pushed and dumped in a circle under the boost of the spiral disc, forming a continuous and uninterrupted coil.
1.2 Analysis of the forces on the spitting machine in the spitting process
During the high-speed rotation of the hollow shaft of the spitting machine, the wire slides relatively in the spitting tube. In the relative motion of the inertia, centrifugal force and friction between the wire and the spit tube, the original linear motion of the wire will be gradually bent into a coil according to a certain curvature, and smoothly and evenly dumped on the air-cooled roller path. During the work of the spitting machine, the spitting machine is mainly subjected to the driving force and friction of the spitting disc on the wire, the friction of the spitting tube on the wire, the centrifugal force of the spitting tube rotating at high speed and the friction between the mill pinch rollers and the wire. In the ideal state of the spooling machine, there is no friction between the spooling disc and the wire, and there is no pushing force of the spooling disc on the wire. The centrifugal force of the spit pipe on the wire, the frictional force of the pinch roller on the wire and the frictional force of the spit pipe on the wire are in an ideal balance, and the frictional force between the wire and the spit pipe is evenly distributed along the vertical tangent of the spit pipe, so that the inner wall of the spit pipe is evenly worn. However, in actual operation, due to the clamping rollers and spitting disc on the wire pushing force and the existence of friction between each other, especially in the clamping rollers after the disappearance of the transport power, the force state of the wire has changed greatly, the original balance of forces is broken, followed by a variety of uneven wear, spitting machine normal spitting state will also be changed, resulting in small and large circles or cause accidents.
2 spitting machine vibration exceeds the standard analysis of the causes
Due to the strong centrifugal force, the vibration phenomenon is unavoidable in the operation of the spitting machine. Spitting machine spitting disk, spitting tube and other components between, mainly by high-strength bolts, pipe clamps, etc. fixed. The root cause of the vibration of the spitting machine exceeds the standard is due to loose fasteners, mechanical parts wear and tear and break the mechanical dynamic balance.
2.1 Spitting disk deformation serious
In the operation of the spitting machine, the spitting disk and the wire between a certain amount of friction. Under the action of this friction, it will gradually lead to the spitting disc wear deformation. When the disc is seriously deformed, the surface of the disc is no longer flat and the coils wound on the disc can cause serious bouncing when they come into contact with the disc. At the same time, due to the wear and deformation of the outer circular surface of the spit disc, the air around it is driven to form stronger airflow and air fluctuations when rotating at high speed, causing abnormal vibrations in the spit machine. In addition, there is a correlation between the degree of deformation of the spit coil and the spitting temperature, the higher the spitting temperature, the more serious the deformation of the spit coil [1].
2.2 The inner wall of the spit pipe is severely worn
The inner wall of the spitting tube is in contact with the high temperature spitting wire friction for a long time, which can easily produce excessive wear and abnormal wear. Excessive wear is generally in the normal state of wear, due to the amount of spit tube production line material is too large or a long period of repeated wear and tear of the inner wall of the spit tube wear over the limit. This wear phenomenon occurs in smaller but more frequent production processes. Abnormal wear is in the case of continuous production of different specifications of wire, due to the different specifications of the spitting diameter, spitting speed, etc., and the spitting tube wall wear of different degrees. Abnormal wear is mainly manifested by a “W” shaped section of the inner wall of the spit pipe. When the inner wall of the spool is severely worn, the trajectory of the wire in the spooling machine tends to shift more severely. This will not only lead to a substandard shape of the wire roll, affecting the quality of the product, but will also increase the vibration and wear of the equipment [2].
2.3 Spooling machine out? At the pallet position offset
When the spooling machine is in operation, the coils rub against the pallet at the exit of the spooling machine to ensure that the coils exit the spooling machine and are ready for the next production stage. However, wear problems can cause the pallets at the exit of the spooler to shift, making them too high or too low. If the pallet position is too low, coil turning is affected. If the pallets are too high, the coils will not move to the next stage of production and will bounce off the pallets. In addition, an offset pallet position can also affect the shape of the coil, causing it to deflect to a lower part of the coil, which is detrimental to the quality of the coil.
2.4 Other causes of vibration overload on the spooler
The spooler has a high degree of continuity and is subjected to high temperature and wear conditions for a long time. This feature also leads to the spitting machine in the work of increased wear and even thermal deformation problems, and lead to the spitting machine lost the original dynamic balance of abnormal vibration. In addition, the wire in a high wire production line has a strong impact effect due to the high kinetic energy. If the spooler is rigid and cannot adjust its deformation according to the production rhythm, it will also cause the spooler to vibrate beyond its limits.
3 Measures to reduce vibration on spinning machines
3.1 Standardised equipment installation steps
A rigorous installation is the fundamental key to ensuring the smooth operation of the spooler and avoiding abnormal vibrations in the spooler [3]. This requires equipment installers to standardize the operation when installing equipment to ensure the accuracy of the installation of the spitting disc, spitting tube and other components. When installing the spit pipe, the centre of the pipe mouth should be ensured that the distance between the centre of the pipe mouth and the outer disc surface of the spit machine is not less than 28cm to ensure that the outer disc surface avoids contact with the coil and wear when the equipment is in operation, preventing the resulting vibration from exceeding the standard. In the installation of equipment, but also to ensure that all parts (especially some rotating parts) firmly combined, spitting machine on the outer disc of the seat tube and spitting tube must ensure that all parts match each other, such as can not match, then other spitting tube should be replaced for installation, do not use mandatory measures.
3.2 Strengthen the daily maintenance of the equipment
Daily maintenance of the equipment is the key to reducing wear and vibration and ensuring good mechanical operation of the equipment. First of all, the vibration value of the spitting machine should be monitored in real time and its vibration situation should be closely monitored. When the vibration value exceeds 8 mm/s, the equipment should be checked and the dynamic balance of the rotor of the spitting machine should be readjusted to effectively control its vibration and prevent it from increasing. Secondly, according to the production rhythm and the operation of the equipment, the clearance between the outer disc protective cover and the outer disc of the spit machine should be checked and measured every few days and the measured values compared with the normal standard values. If this clearance level exceeds 3mm, it means that the gap between the two is too large and may cause vibration overload, requiring prompt restorative adjustment of the eccentricity of the outer disc and a reset of the power balance of the spitting machine. Thirdly, if the inspection reveals that the spitting tube has reached its specified age, the spitting tube should be replaced. After replacement, the vibration value of the spitting machine should be tested and adjustment measures should be taken to ensure the dynamic balance of the equipment and to minimise the vibration level of the spitting machine.
3.3 Do a good job of lubrication and cooling of the equipment
Good lubrication is an important measure to ensure the smooth operation of machinery and equipment and eliminate bad wear. Should be based on the type of spitting machine and the use of requirements, the choice of high-temperature viscous lubricants, spitting machine bearings and other parts of the lubrication maintenance, to ensure that the bearings are well lubricated, to improve the stability of the spitting machine operation. In addition, in order to prevent the equipment from running at too high a temperature and lead to coil deformation, lubrication failure and other problems, should also be configured with the appropriate cooling facilities to prevent equipment overheating. In practice, water cooling is mostly used for cooling. When using, attention should be paid to the cleanliness of the cooling water and the pH value to avoid corrosion and pollution of the equipment. Reasonable setting of cooling water flow and pressure to ensure good cooling effect.
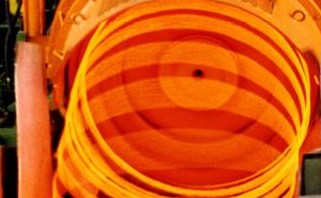