The beneficiation plant has 2 sets of self-centred vibrating screens, which bear the responsibility of screening the crushed ore and play a very important role in the production of the crushing system and the production of the main field house.
1、Existing problems
(1) Due to the high speed operation of vibrating screen, the lubrication requirement for bearings is high. The original design is defective and there is no refuelling position, resulting in poor lubrication of the bearings, frequent heating phenomenon and accelerated damage to the bearings.
(2)The original seal is the structure of bearing cover and sealing ring, weekly dismantling and refuelling, we have to dismantle the big pulley and counterweight wheel, resulting in maintenance labor intensity, and easy to damage the pulley, counterweight wheel, so that the consumption of spare parts is large.
(3) Frequent damage to bearings is not only detrimental to production, but also causes damage to the bearing housing which is matched with the bearings due to dismantling, resulting in waste.
2、Renovation programme
Aiming at the above problems, we carry out the following transformation:
(1) Replace the original device bearing cover and sealing ring with bearing gland sealing, and add 2 skeleton oil seals.
(2) The refuelling position is changed to inside the hollow shaft sleeve of the screen body, and water-cooling device is added, so that it is not necessary to dismantle the two ends of the shaft, which is very convenient and well lubricated.
3、Effects after transformation
Through the operation, the transformation effect is good.
(1)Bearing lubrication is good, no oil leakage phenomenon, prolong the bearing life.
(2) Normal operation, the failure rate is greatly reduced, saving a lot of spare parts and materials.
(3) Maintenance and overhaul are convenient, and the labour intensity is very small.
4、Economic benefits
(1) Direct economic benefits after the transformation of the annual savings of spare parts and materials costs 52,500 yuan (of which 22,000 yuan eccentric shaft, 3626 bearings 18,000 yuan, 8,000 yuan counterweight wheel and pulley, bearing seat 3,000 yuan, oil savings of 1,500 yuan).
(2) Indirect economic benefits reduce the labour intensity of maintenance, reduce the breakdown and downtime rate, and create conditions for smooth operation of production.
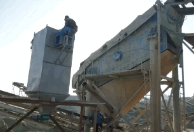