Belt conveyors are a major piece of machinery in many projects, as they have many advantages in transporting materials and are favoured in the process of warehousing and discharging grain. However, the belt conveyor in the process of material transportation, there are more problems, such as belt deviation, spreading material, etc., these problems have a great impact on the efficiency of the belt conveyor, today to talk about the belt conveyor operation of common failures and solutions.
01 Causes of belt deviation
The belt deviation phenomenon occurs during the installation process. There are three main reasons for this. Firstly, the frame of the belt conveyor is tilted, for example, the centre line of the frame deviates from the normal position, and the two sides of the frame have a high and low tilt, etc., which may cause the belt to deviate. Secondly, as the joint between the conveyor belts of the belt conveyor is not straight, so that the tension at the two ends of the belt is not the same, in this case, the belt will generally tilt in the direction of greater tension, so that the phenomenon of deviation occurs. Thirdly, the guide trough of the belt conveyor may also cause the phenomenon of runout. The rubber plates on both sides of the guide trough produce different sizes of pressure on the belt, thus making the belt of the machine suffer from different sizes of resistance, which finally causes the phenomenon of runout.
The runout phenomenon occurs during the operation process. Firstly, after a period of operation, the belt conveyor will be stained with some mineral powder on the drums and rollers, and after accumulation, the cylinder diameter of the drums and rollers will become bigger, making the tension at each position unequal in the running process, thus causing the deviation. Secondly, aging and deformation of the belt will also cause deviation. Thirdly, the uneven weight distribution of the various materials running on the belt conveyor may also cause deviation. Fourthly, the vibration phenomenon in the running process is also an important cause of runout.
02 Measures for belt deviation
-Adjust the roller set

The diagram above shows the force analysis of the load bearing rollers of a belt conveyor when installed with deflection.
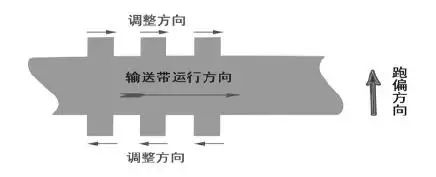
Fig. 2 Adjustment diagram
The main reason for machining the mounting holes on both sides of the roller support into long holes is to facilitate the adjustment of the roller set. This adjustment method is generally used to deal with belt deflection caused by skewed frames, uneven distribution of ore and other reasons.
-Adjustment of the drive pulley and redirecting pulley position
A belt conveyor has at least 2 to 5 rollers, which are installed perpendicular to the centre line of the belt conveyor in the length direction. As shown in the diagram.

Fig. 3 Installation diagram
Adjustment of the position of the drive pulley and the diverter pulley. The specific direction of adjustment corresponds to the direction of runout of the drum, e.g. if the runout is to the right, the right-hand bearing is adjusted. When adjusting the tail pulley, the operation is reversed in the same way as the head pulley adjustment.
-Cleaning the drum surface or replacing the drum

Fig. 4 Analysis of drum running forces
As shown in the diagram, there are many factors that can cause the diameter of the drum to become larger, such as wear on the surface of the drum, or other objects sticking to the surface of the drum, making the diameter of the drum different at different locations. FQ is the traction force of the drum conveyor, and during the operation of the drum, a partial force FY is generated in the direction of the larger diameter, resulting in a runout. For this reason, regular cleaning of the pulley or replacement of the pulley will solve this type of fault.
-Adjustment of the belt tension to solve the problem of belt deflection
When dealing with belt deflection due to belt tensioning problems, it is similar to dealing with drum deflection. The bearings are adjusted according to the specific direction of belt deflection, depending on which side of the belt is being adjusted. In addition, the runout can also be changed by making improvements to the equipment, for example by using a new type of carrier roller set. The load-bearing roller set is a forward-tilting structure and the unloaded roller set is a V-shaped structure, both of which are very effective in dealing with belt runout on belt conveyors.
Handling of belt runout on bi-directional belt conveyors
The bi-directional belt conveyor deviation phenomenon is more difficult to handle than the general belt conveyor, in operation, it is usually adjusted in one direction first, and then in the other direction.
03 Analysis of spreading problems and measures to solve them
Spreading of material at the transfer point of the belt conveyor. Control the amount of transport, strengthen the usual maintenance and maintenance of the conveyor to.
Spreading of material when the belt deviates. It can be solved according to the above-mentioned measures for dealing with belt runout problems.
Spreading caused by overhanging belts in the concave section. The machine should be designed to increase the radius of curvature of the concave section.
The size of the radius of curvature of the convex section also has an influence on the material transport of the belt conveyor. When the value of the groove angle is greater than 40°, the phenomenon of chipping or folding may also occur in other parts of the belt conveyor. To deal with this problem, the size of the groove angle should be reduced accordingly or the interval between the length of the transition zone should be lengthened accordingly, so that the groove angle of the belt can be slowly transitioned to avoid the phenomenon of folding or arching due to sharp transition. Alternatively, the radius of curvature of the belt cams can be increased to solve these problems.
04 Analysis and treatment of abnormal noise problems and belt slippage
Noise caused by off-centre rollers. During the operation of the belt conveyor, the rollers are noise-prone devices and are accompanied by periodic vibrations. The noise is caused on the one hand by the uneven thickness of the seamless steel wall in the manufacturing process of the rollers, which results in a relatively large centrifugal force, and on the other hand by the large deviation from the centre of the bearing holes at both ends and the centre of the outer circle during the processing of the rollers, which also results in a relatively large centrifugal force and thus an abnormal noise. To deal with the problem of abnormal noise, first check the bearings of the belt conveyor, if the bearings are damaged, replace them, if they are not damaged, take other ways to deal with them.
For the noise problem caused by different shaft centres of the coupling, the position of the motor’s reducer can be adjusted accordingly to solve the problem.
For abnormal noise caused by the drum, it is usually caused by damaged bearings, so the bearings can be replaced. For the phenomenon of belt slippage, if it is the slippage of a heavy hammer tensioning belt machine. It is possible to add counterweight until the belt does not slip, but it should be noted that the tension should not be too much to avoid too much tension instead of affecting the service life of the belt. In the case of spiral tensioned or hydraulically tensioned belts, slippage can be avoided by adjusting the tensioning stroke. The tensioning force can be increased by adjusting the tensioning stroke, but it should be noted that this treatment may result in permanent deformation of the belt, which can be followed up by cutting off the deformed belt.
05 Conclusion
Belt conveyors are a relatively common machine in production life, and are currently widely used because of their large conveying capacity, relatively low power consumption and their adaptability to various materials. But the belt conveyor in the process of operation will also appear some faults, such as belt deviation, belt slippage, noise, etc., to solve these problems, according to the cause of the problem to take the appropriate way to solve.