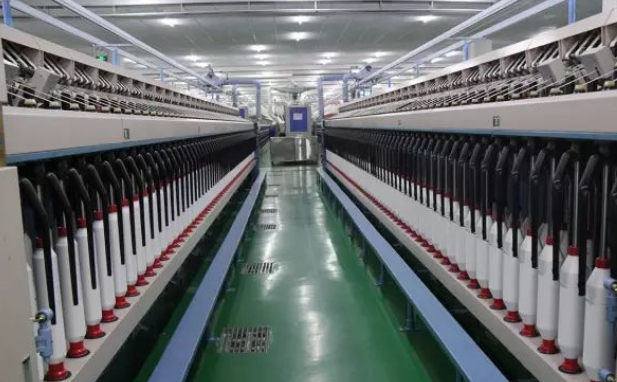
Yancheng Industrial Vocational and Technical College purchased two FA458 roving frames in 2002. Since its operation, the overall operation is good, the failure rate is low, and it is easy to maintain. However, the winding drive and electrical control system often have electromagnetic clutch, brake, two-way iron suction, reversing gear, travel switch, and gun belt reset mechanism and other failures. In order to improve the utilization rate of equipment and reduce the failure rate, the frequent failures of the winding drive and electrical control system of FA458 roving frame and the treatment measures are summarized.
1 Composition and function of winding drive system
The winding drive system of FA458 roving frame is composed of a gun speed change device, a differential device, a swing device, a lifting device and a reversing device. The speed change device of the iron gun is composed of the upper iron gun and the lower iron gun. Its function is to change the input constant speed into a speed change motion that decreases layer by layer with the increase of the winding diameter of the bobbin by changing the transmission ratio of the input shaft and the output shaft. The differential device is located on the main shaft, which is an epicyclic gear train, including the first wheel, the last wheel, and the swivel arm. Its function is to combine the constant speed from the main shaft and the variable speed from the lower iron gun, and complete the winding of the bobbin through the swing device. The swing device is located between the output synthetic speed gear of the differential device and the shaft end gear of the bobbin. Its function is to transmit the output speed of the differential device to the bobbin that rises and falls with the keel. The lifting device is composed of keel, balance mechanism, lifting lever, lifting shaft, keel force electromagnetic clutch, keel force motor and rack type lifting device. Its function is to make the lifting keel move regularly. The reversing device is composed of full yarn self-stop, iron gun belt reset, reversing proximity switch, programmable controller PLC, two-way iron suction and reversing gear. The full yarn self-stop is composed of full yarn positioning travel switch SL7, switch contact of length meter and brake; The iron gun belt reset mechanism is composed of belt reset travel switch SL13, belt tension travel switch SL14, belt reset motor and belt reset electromagnetic clutch.
2 Working principle of winding drive system
The main motor of FA458 roving frame drives the main shaft through the rubber synchronous belt. The 55-tooth gear on the main shaft drives the 46-tooth gear on the spindle shaft through the rubber trapezoidal synchronous belt, thus driving the spindle wing on the keel on the spindle shaft to rotate at a constant speed. The bobbin speed is composed of the constant speed of the main shaft and the variable speed of the variable speed mechanism. The constant speed of the main shaft drives the active iron gun through the twisting stage gears Z1, Z2 and the twisting gear Z3. The active iron gun drives the passive iron gun through the belt, Move the position of the belt, and the speed change of the passive iron gun will be divided into two outputs through the winding gear Z13, one of which is transmitted to the first wheel of the differential device through the 29-tooth gear. The differential device will combine the constant speed from the main shaft and the speed change from the lower iron gun. The combined speed will be transmitted to the oscillating device through the 45-tooth gear of the differential device, and finally to the bobbin through the oscillating device, To complete the winding of bobbin. The other way drives the lifting shaft through the lifting stage gears Z9, Z10, lifting transformation gear Z11 and reversing gear, controls the lower keel on the lifting shaft to complete the lifting action of the lower keel. When the lower keel is lifted to the reversing position, the keel reversing device makes the sensing iron deflect to the left or right. When the sensing iron deflects to the left or right, the keel up or down proximity switch generates the sensing signal, which is transmitted to the PLC CPU through the PLC input terminal, The CPU generates an output signal to control the bidirectional iron suction of the reversing device, and controls the reversing gear in the reversing box through the bidirectional iron suction to complete the reversing action, and then drives the chain pulley type keel lifting device to complete the lifting action of the keel through the coordination of the keel force motor and its electromagnetic clutch.
3 Working principle of doffing control system
During normal spinning, when the counter sends a full tube signal, the switch contact of the length meter is connected, and the full tube signal light is on. When the contact contacts the travel switch, the circuit is connected, so that the main motor and the suction motor stop rotating and stop automatically. After the machine stops stably, it starts a series of doffing actions.
(1) Belt reset action: the belt reset motor rotates counterclockwise, and the belt reset electromagnetic clutch is powered on. At this time, under the drive of the belt reset motor, the lower cone is lifted by the mechanical transmission mechanism, and the belt is relaxed and restored to the initial spinning position. After touching the belt reset travel switch SL13, the belt reset motor and the belt reset electromagnetic clutch are powered off.
(2) Dragon rib over-lowering action: after the belt reset action is completed, the dragon rib over-lowering action begins. The dragon rib forced motor rotates clockwise, and the dragon rib drive electromagnetic clutch loses power at the same time for 1s. When the dragon rib forced electromagnetic clutch is powered on, the dragon rib begins to over-lower. After the dragon rib bottoms, the action stops after hitting the dragon rib bottoming travel switch SL11.
(3) Belt tension action: after the dragon rib over-lowering action is completed, the belt reset motor rotates clockwise, the belt reset electromagnetic clutch is powered on at the same time, the lower cone wheel is dragged down by the belt reset motor, and the belt tension travel switch SL14 is pressed, then the belt tension action stops.
4 Typical fault analysis and treatment of winding system
4.1 Electromagnetic clutch failure
The FA458 roving frame has four electromagnetic clutches, which are brake (DLM3-1.2A), belt reset electromagnetic clutch (DLM3-2.5A), rib forced electromagnetic clutch (DLM3-1.2A), and rib drive electromagnetic clutch (DLK1-5AF). DLM3 series electromagnetic clutch is a wet multi-plate electromagnetic clutch, and DLK1-5AF type electromagnetic clutch is a dry multi-plate electromagnetic clutch. Their principle is coil? Magnetic force is generated when electricity is applied to close the “armature” plate, and the clutch is engaged; When the coil is powered off, the “armature” bounces back and the clutch is in the separation state. In several years of maintenance practice, we have concluded that the failures of the doffing control system of FA458 roving frame are mostly caused by the failure of the electromagnetic clutch, while the failures of the electromagnetic clutch are mostly caused by the slipping and failure of the electromagnetic clutch due to the wear of the friction plate, as well as the open circuit of the coil due to the overheating or short circuit of the coil. Therefore, we will focus on the treatment methods and maintenance measures of the friction plate wear and coil open circuit. 4.1.1 Troubleshooting of friction plate of electromagnetic clutch
Some electromagnetic clutches are installed on the second wallboard of the third car stop, some are installed on the forming device of the third car stop, and some are installed in the front of the car, which has high environmental requirements. Because there are many flying flowers and short fluff in the roving workshop environment, the electromagnetic clutch must be cleaned regularly to remove the anti-rust grease and sundries; You must also check the length of the “armature” stroke of the electromagnetic clutch at regular intervals and check the tightness of the bolts, that is, tighten the electromagnet, electromagnet and shell, magnet yoke, electromagnet coil and wiring bolts; Especially for the DLK1-5AF dragon rib drive electromagnetic clutch, the minimum clearance between the brake surface and the rotary table needs to be adjusted when it runs continuously for 3 to 6 months. Otherwise, the electromagnetic clutch will often slip, ignite and cannot be disengaged during the production process. Due to the severe wear and frequent failure of the friction plate, in order to reduce the failure rate and improve the work efficiency, we use DLM-80C single-plate electromagnetic clutch to replace the original DLK1-5AF dry multi-plate electromagnetic clutch (Dragon Drive electromagnetic clutch). After more than one year of use practice, the clutch has the characteristics of simple structure, convenient transmission, small maintenance workload, and the most important thing is to basically eliminate the slipping and unstripping faults, and improve the production efficiency.
4.1.2 Handling of electromagnetic clutch open circuit fault
Coil open circuit caused by coil short circuit or overheating is also a common fault type of electromagnetic clutch. During maintenance, most maintenance personnel believed that the reason was that the solenoid coil was burnt out and the maintenance measures were taken to replace the solenoid coil. However, after several years of production practice, it was found that most of these failures were caused by the loose or disconnected part of the coil lead wire and the slip ring welding, resulting in poor contact or burning at the joint.
Therefore, in case of coil open circuit fault, do not easily judge that the coil is burnt out and replace the coil. Pry the epoxy resin on the surface of the coil, find out the lead head, and then carefully check the connection between the copper ring and the coil lead. If the joint is disconnected, use soldering tin to weld it; Or weld the coil lead out with a wire, drill an M4 screw hole on one side of the copper ring, and finally connect the lead with the copper ring with screws. Using this method to repair the coil open circuit fault can not only achieve rapid maintenance, but also save maintenance costs.
4.2 Dragon bar reversing device failure
The rib reversing device of FA458 roving frame often has faults such as the rib does not rise, does not fall or the rib rises during normal driving, the clutch belt slips when it falls, the rib forced motor does not work, and the rib does not reverse when it moves up or down to the reversing point. Therefore, we will focus on the treatment and maintenance measures of three kinds of faults: two-way iron suction, reversing proximity switch and reversing gear.
4.2.1 Two-way iron absorption fault
The bi-directional iron suction is installed in the front of the vehicle. There are two coils in the bi-directional iron suction. When the different coils are energized, the piston will be drawn to the left or right. The common faults of the two-way iron suction are that it does not close when it is powered on, does not release when it is powered off, or releases slowly, the electromagnetic attraction is insufficient, and the coil is overheated or burnt. It is easy to deal with the failure of power-on without closing, power-off without releasing or slow release and coil overheating or burning, but the failure of insufficient electromagnetic attraction is often ignored. For example, when the FA458 roving frame spins to about 1650m, there will be “yarn blowing” at the lower edge of the roving. The mechanic checks that the machine has no fault. After careful inspection, the electrician finds that the electromagnet can not be moved by hand when it is powered on, but it can be moved by hand when it spins to the lower edge. Therefore, it is judged that the problem is the insufficient suction of the two-way iron suction. After replacing the two-way iron suction, the fault is eliminated and the production can be started normally. 4.2.2 Reversing proximity switch fault
FA458 roving frame has two reversing proximity switches, and the clearance between them and the induction iron should be kept between 2mm and 5mm. Therefore, it is necessary to regularly check and repair the two reversing proximity switches. During the inspection, wipe off the water and dust on the sensor first, use metal objects (screwdriver, wrench, etc.) to repeatedly approach the end of the sensor, and observe whether the signal indicator light flashes. Move the sampler so that the sensor is directly opposite the sensing block, and check whether the gap is too large. If the gap is too large, the sensor cannot give a signal. If the output signal of the sensor is normal, check whether the signal line is normal. First, check whether the power supply of the sensor is normal, and then check whether the signal line entering the PLC is normal.
4.2.3 Reversing gear failure
When the keel movement reaches the reversing point, if the bidirectional iron suction action, it means that the reversing proximity switch and the bidirectional iron suction are not faulty, then the keel reversing fault may be caused by the reversing gear. First, check whether the two limit bolts on the reversing box that limit the swing rod travel are properly adjusted, whether the spring on the swing rod is damaged, whether the shaft at the lower part of the box is closely matched with the swing rod connecting key, and whether the teeth on the left and right bevel gears are fully engaged with the clutch; Then check whether the gear bearing or gear is damaged; If the fault still exists, use a multimeter to check whether there is a fault in the dragon force motor and the dragon force electromagnetic clutch.
4.3 Travel switch fault
The travel switch of the rib reversing and doffing control system of FA458 roving frame includes the full-yarn positioning stop travel switch SL7, the belt reset travel switch SL13, the belt tension travel switch SL14, and the rib lowering travel switch SL11. If the full-yarn self-stop mechanism is faulty, check the position of full-yarn positioning stop travel switch SL7, and adjust the full-yarn positioning stop travel switch SL7 to just be pressed by the upper edge of the right fender; If the belt reset mechanism is faulty, check whether the shift fork of the travel switch SL13 can work normally with the release of the belt; If the lifting mechanism of the keel is faulty, adjust the bottom travel switch SL11 of the keel so that it is just pressed by the lower edge of the right fender; If the belt cannot be tensioned, check the position of the belt tension travel switch SL14, that is, restore the belt to its original position, turn the handwheel to tension the belt, and adjust the belt tension travel switch just to be hit. Example of fault maintenance: During a fault handling, the turnman reported that the FA458 roving machine could not be opened. After inspection, it was suspected that the lower limit travel switch SL9 of the rib was faulty. According to the status display on the display of the failed roving machine and the non-failed roving machine, it was found that the normally closed contact of the lower limit travel switch SL9 of the rib was not closed and was always in the open state. For this reason, we found the position of the lower limit travel switch SL9 on the roving frame according to the drawing, and can start normally after replacing the travel switch.
4.4 Photoelectric switch failure
FA458 roving frame has two sets of broken yarn photoelectric switches, which are installed on the upper rib surface; A set of broken strip photoelectricity is installed on the rear strip guide frame; Two sets of dragon rib photoelectric switches are installed on the second front wall panel and the rear wall panel; The two groups of protection photoelectric devices adopt the “one transmitter and two receivers” mode, that is, one transmitter and two receivers are installed at the front and rear of the vehicle. Example of fault maintenance: once the turn-breaker reported that the FA458 roving frame could not be started, the blue light of the five-color signal light was on, the two groups of broken yarn photoelectric switches were on all the time, and the inching drive was normal, but when the normal drive was started, a broken yarn photoelectric switch in front of the car would flicker. After carefully finding the cause, it was found that the flying flowers on the roving tube made the broken yarn photoelectric receiver unable to receive the infrared light and sent out a high-level signal, which was processed by the CPU of PLC and sent out a signal to control the positioning and stopping of the roving frame spindle wing. To handle this kind of fault, you only need to remove the flying flowers on the roving tube, press the stop button to reset the blue light of the five-color signal light, and then press the start button to start the normal driving.
4.5 Dragon rib lifting failure
The lifting failure of the keel is usually caused by the following conditions: the lifting chute, chain, lifting gear and rack are not clean; Poor engagement of lifting gear and rack; The chain and lifting chute (head, middle and tail) taper pulley belt moving guide rail is lack of lubricating oil; The set screw of lifting gear does not work; The clearance between the iron gun and the iron gun shaft is too large. In case of rib lifting failure, first clean the lifting gear, rack, lifting chute and chain, and check the meshing of lifting gear and rack; Then add lubricating oil to the chain, lifting chute and bevel pulley belt moving guide rail, and check whether the lifting gear set screw is loose; Finally, check the clearance between the iron gun and the iron gun shaft. If the clearance is too large, the set screw will be loose. If the wear clearance of the inner hole of the iron gun is too large, the iron gun shaft must be replaced. If the problem still cannot be completely solved, it should be replaced with the upper iron gun.
4.6 Differential case gear failure
This kind of fault is shown as the phenomenon of roving “rising”, which may cause all “rising” of doffing and the broken ends are at the palm. It is analyzed that the main causes are gear wear and bearing damage in the differential case. When the gear in the differential box is not seriously worn, the tension will be normal for a while and abnormal for a while, resulting in poor roving formation; When there is no clearance between the gears at the end of the iron gun in the differential box, which makes the gears unable to run, the roving will all “rise” and break, and the lifting speed of the dragon rib will also be affected, resulting in all “rise” of the roving. Of course, the cause of this kind of failure may also be related to other parts of the transmission mechanism. When checking the differential gear box, drain all the oil and observe whether the oil is blackened and whether there are fine iron particles in it.
5 Maintenance principles of roving frame
Based on the analysis of common faults and treatment measures in the winding system of FA458 roving frame, it is considered that in order to do a good job in the maintenance of roving frame, the maintenance personnel must understand the basic principles of mechanical transmission and electrical control; We should have a certain hands-on ability, and also be good at analyzing the causes of failures and summarizing maintenance experience.
In the process of production, when the roving machine breaks down, the turner is required not to doff the yarn when the machine breaks down, and keep the site for the purpose of analyzing the cause of the fault. If the car breaks down during doffing, it is necessary to find out whether the fault occurs in the belt reset stage, the rib over-lowering stage, or the belt tension stage, so as to determine the position or element causing the fault. The maintenance of electrical equipment faults should focus on hearing, seeing and measuring; To repair the motor fault, first check whether the motor has a cooling fan and whether there are flying flowers winding inside the fan. Second, add grease to the motor bearing in time to ensure sufficient lubrication to extend the service life of the bearing. At the same time, the maintenance of the roving frame is also very important. The important parts should be checked regularly to see if the screws are loose and make abnormal noises. The connection points, contact points and control buttons should be cleaned regularly. Due to the high failure rate caused by the power supply, it is necessary to check whether the power supply is normal before maintenance, which can achieve twice the result with half the effort. When roving machine faults and debugging coexist, the faults should be eliminated first, and then debugging, and debugging must be carried out on the premise that the electrical control circuit is normal.
6 Conclusion
To sum up, the causes of common faults in the winding drive system and electrical control system of FA458 roving frame are summarized, such as electromagnetic clutch fault, rib reversing device fault, travel switch fault, photoelectric switch fault, differential gear fault, rib lifting fault, etc., and corresponding solutions are proposed. For some frequent failures, such as severe wear of the friction plate of the electromagnetic clutch, the use of DLM-80C single-plate electromagnetic clutch instead of DLK1-5AF dry multi-plate electromagnetic clutch (Dragon Drive electromagnetic clutch) effectively reduces the equipment failure rate and maintenance workload. Due to the variety and complexity of roving frame fault phenomena, maintenance methods and maintenance means, the existing maintenance experience can be used for reference, but the specific problems must be specifically analyzed. In short, according to the characteristics of the roving process environment, the cleaning and maintenance of the roving frame during daily use should be done well. To ensure the long-term and efficient operation of the roving frame, on the one hand, the quality of the maintenance personnel should be improved; On the other hand, a strict cleaning, maintenance and maintenance management system should be formulated, which is the key to solve the problem.