The bearings were air-cooled after hot mounting and the inner rings were found to be cracked. For this reason, the inner ring of the cracked bearing was subjected to chemical composition analysis and metallographic examination to reveal the cause of inner ring cracking. The results show that the chemical composition and low-fold organisation of the inner ring of the bearing are qualified, but there is a bad organisation of Torrite present, which reduces the strength of the inner ring and leads to its cracking.
In the process of industrial gearbox operation, the bearing is one of the very important parts in the mechanical operation. As a bearing and rotating parts, bearing damage leads to other related parts chain damage caused by the loss is very alarming. For this reason, bearing failure analysis and related preventive measures are very important.
1 Physical and chemical inspection
1.1 Macro test
Taiyuan Heavy Machinery Group Gear Transmission Branch purchased two sets of bearings after hot installation of natural cooling, the next day found cracked. The set of cracked bearing inner ring size of 260mmx480mmx130mm (see Figure 1), the cracked part of the bearing inner ring, the crack is perpendicular to the circumference, has been completely disconnected, as shown in Figure 2. Cutting the bearing inner fracture dissection, you can see that the section is flush, the crack began on one side of the end face, is a typical overstress brittle fracture, as shown in Figure 3 [1]. Bearing inner ring longitudinal specimen acid immersion test did not find other defects, it can be seen that the bearing inner ring low times the organisation is qualified, as shown in Figure 4 [2].
1.2 Chemical composition analysis
The fractured bearing inner ring was analysed for chemical composition, and the results are shown in Figure 1. From Table 1, it can be seen that the bearing material meets the bearing steel material requirements.
1.3 Hardness test
The inner ring of the fractured bearing is subjected to hardness test and the results are shown in Table 2. From the test results in Table 2, it is known that the hardness of the inner ring of the fractured bearing is qualified.
1.4 Microstructure observation
Samples were taken from the cracked inner ring of the fractured bearing for microstructure observation and the results are shown in Table 3 and Figures 5 and 6. From the test results, it can be seen that the purity of the bearing inner ring is qualified, carbide qualified, but the microstructure out of Torrhenite, is quenched underheating organisation [3].
2 Analysis and discussion
Shaft and bearing inner ring with hot mounted base hole system interference fit. Usually heavy-duty products are required to have a large amount of interference, in order to prevent slippage in the work, but when the amount of interference is too large, it will directly lead to overstress brittle fracture. Excessive interference for the bearing inner ring hole processing size is small or large shaft. In addition, after the installation of positioning, if the two coaxial deviation is large, but also the inner ring end face directly increase the fact that the amount of interference, caused by overstress brittle fracture.
Bearing material organisation of the inner ring of the torus, is quenched underheating the formation of defective organisations. Although the macro hardness value is qualified, but the micro-hardness of Toledo is lower than the tempered martensite, the direct formation of microscopic soft spots, reducing the mechanical properties of the material, especially the later use of the process of contact fatigue resistance is poor, easy to cause early pitting. In addition, Trochoidal organisation has a certain effect on the fracture strength of the material, after hot loading may also have a certain role in promoting cracking.
3 Conclusion
Through the bearing inner ring fracture degree of macroscopic detection, microstructure observation, chemical composition analysis, hardness testing and other methods, the fracture bearing cracking cause analysis, found that the fracture bearing inner ring material qualified, purity qualified, densification, uniformity is good. The cracking of the inner ring of the bearing is overstress brittle fracture after hot installation, which is caused by the excessive stress formed by the interference fit. The source of overstress may be too large for the amount of interference, installation of coaxial deviation. In addition, the material in the trachyte organisation has a certain effect on the fracture strength of the bearing, after hot installation may also have a certain effect on the promotion of cracking.
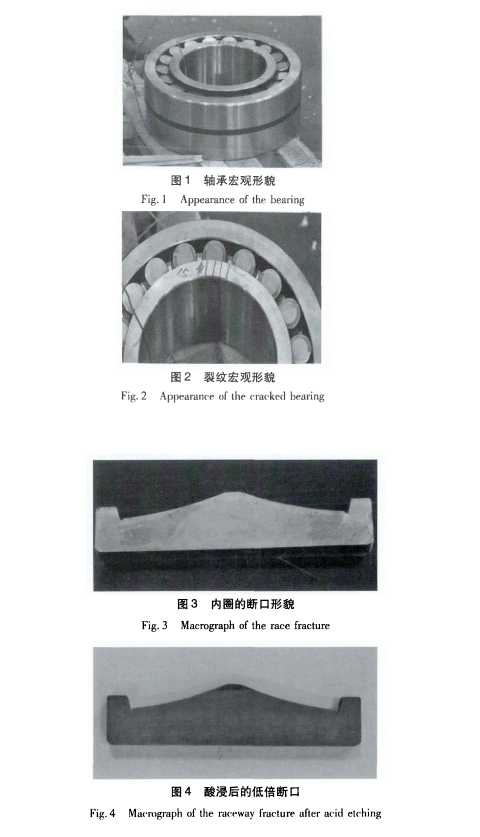