Introduction The analysis, diagnosis and troubleshooting of automated machine tools can significantly improve the efficiency of machine tool applications and enhance the productivity of machine tools. Relying on the analysis and diagnosis of a series of common faults in automated machine tools, can help to effectively improve the efficiency of troubleshooting, further promote the speed of troubleshooting, and promote the safe and orderly operation of automated machine tools. Thus, the research on the troubleshooting technology of automatic machine tools has very important practical significance.
1 Overview of automated machine tools
Automatic machine tools, also known as CNC machine tools, refers to a modern equipment, high technology and manufacturing can achieve automatic management of the adjustment of the machine tool model. In an automated machine tool, a regulation system is installed which enables the logical processing of programmes with control codes or other symbols, their decoding and transmission to the numerical control by means of an information carrier [1]. The signals are then sent out via the numerical control to control the operation of the machine. Automated machine tools are ideally suited to the processing of precision parts and are an important development in modern machine tool control technology because of their reliable performance. Compared to traditional machine tools, automated machine tools have a series of advantages, such as high precision, adaptability, high efficiency, the emergence of automated machine tools to a large extent to promote the modern development of production equipment.
2 Automatic machine tool fault analysis and diagnosis
In order to carry out research on automatic machine tool troubleshooting technology, the first step should be to carry out the corresponding analysis and diagnosis of the fault, so as to provide a strong basis for the maintenance personnel to select the appropriate troubleshooting technology. The analysis and diagnosis of faults in automatic machine tools includes a number of different aspects, namely consultation and investigation, on-site testing, analysis of the causes of faults, determination of the causes of faults and preparation for troubleshooting [2]. First of all, when receiving information about a fault in an automatic machine tool, the operator should be asked not to do any processing of the fault state on site as far as possible, and to carry out a consultation and investigation in the first instance to prepare for the fault analysis. Then, the overhauler should combine a range of information provided by the operator to verify the accuracy of the initial assessment; due to the limited level of the operator, so the description of the fault condition is vague or completely inaccurate, so the overhauler arrives at the scene still can not rush to deal with, but should carry out a re-investigation of the situation, so as to prevent damage to the site, making troubleshooting more difficult This prevents damage to the site and makes troubleshooting more difficult. Next, the overhauler should combine the results of the investigation and testing with a fault analysis in accordance with the fault manual, listing the potential causes of the fault. In the analysis of a series of reasons to carry out re-examination, the final cause of the fault, and finally to carry out troubleshooting before the preparation.
For automatic machine tool fault diagnosis, the common diagnostic methods include: instrumentation, signal and alarm analysis and detection, spare parts replacement and interface detection. Among them, the instrument analysis test method is the use of commonly used electrical instruments on the various groups of AC and DC supply voltage testing, and then find out the potential triggered by the fault. Signal and alarm analysis and detection method is through the work of the indicator, to grasp the operation of automated machine tools, and then find out the relevant components that cause the fault. The replacement of spare parts is the first step in replacing spare parts and then carrying out maintenance of the faulty board. The interface detection method is used to assess the cause of faults by means of the interface signals shown on the output board indicators.
3 Troubleshooting of automated machine tools
3.1 Power supply system faults
The power supply is an important source of power for the operation of automated machine tools. If the power supply system fails during the operation of an automated machine tool, this will inevitably have a negative impact on the orderly operation of the automated machine tool, plus the fact that the power supply system failure is likely to make the relevant data available and thus expose the production operation to significant losses. At this stage, for some developed countries, there is usually no need to test the power supply system as they have an adequate supply of electricity and a very high quality grid. However, in China, as the power supply system needs to be further improved, coupled with the influence of various human factors, this requires the technical personnel in the process of mechanical design, must carry out a good design of the power supply system of machinery and equipment, in order to prevent the failure of the power supply system [3].
3.2 CNC system position ring failure
The position loop failure of the CNC system mainly includes two situations, one is the position loop alarm, which is caused by the damage of the measuring element, the open circuit of the position measuring circuit and the missing interface signal of the position control building. The other is the movement of the co-ordinate axes without command, which is caused by open feedback wiring, excessive drift, or the position or speed loop being connected to positive feedback.
3.3 Inadequate machine dynamics
Insufficient dynamic characteristics of automated machine tools, workpiece processing quality is reduced, or the corresponding speed of the machine tool to produce strange movement. This kind of failure and the mechanical drive system loss of excessive correlation, may also be the key parts of the lubrication effectiveness is not sufficient caused by. For the electrical control system, the position ring, speed ring and optimum condition are accompanied by certain deviations, so the optimum condition should be set again after the fault has been removed.
3.4 Episodic stoppages
One is due to the system software is not designed to make the relevant functions difficult to achieve, and thus cause the automation of machine tool operation failure, this kind of failure can be eliminated by continuing to restart the machine. Another is due to external factors triggered by the automatic machine tool operation failure, such as machine tool working environment temperature is too high, moderately large, external radiation, etc., the part of the external factors also belong to cause episodic downtime failure of the cause, not only will cause adverse effects on the machine tool system, but also increase the machine tool loss, and therefore must improve the effective attention to it [4].
All in all, in production practice, the differences between different lathe models in different production enterprises must be fully considered and the specific reasons for the failure must be analysed. In view of this, the relevant personnel must continue to study and research, summarize experience, improve the effective understanding of the connotation of the characteristics of automated machine tools, strengthen the comprehensive analysis of the automatic machine tool fault analysis and diagnosis, carry out a good automatic machine tool troubleshooting work, and actively promote the safe and orderly operation of automated machine tools.
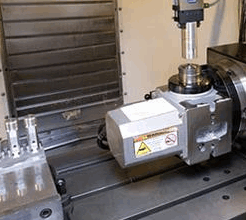