Abstract: There are many transportation links involved in coal mining, and the bridge transfer machine is one of the key intermediate transfer transportation equipment in the fully mechanized mining face. The integrity of the bridge loader directly affects the high yield and safety of the working face. Due to the poor working conditions of the working face, the bridge transfer machine is prone to failure. In view of the different faults of the transfer machine and in combination with the production site, the faults are analyzed and studied, and the corresponding measures are put forward. Through the implementation of effective measures, the failure rate of the transfer machine is greatly reduced, laying a foundation for the efficient production of the working face.
0 Introduction
The bridge transfer machine is an important transfer transport equipment for coal mining. The main function of the transfer machine is to achieve the purpose of coal transfer by connecting the scraper conveyor and the belt conveyor, thus realizing the continuous transportation of coal flow. Arrangement direction: the transfer machine is arranged vertically with the scraper, and parallel with the belt conveyor. Transportation process: the broken coal is transported to the scraper conveyor, then to the bridge conveyor, and finally to the belt conveyor. Due to poor underground working conditions (large dust and high humidity), uneven impact load may also be borne during operation, resulting in different faults in the operation of the transfer machine, affecting the start rate of the transfer machine, and having a negative impact on the mining work of the working face.
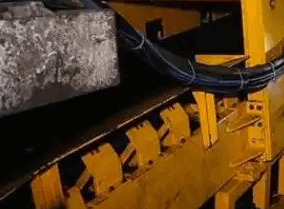
- Structure and working principle of bridge transfer machine
At present, the bridge type transfer machine is a kind of intermediate transfer mechanical equipment that can move longitudinally and is widely used by coal mining enterprises. The transfer machine is arranged in the transportation roadway and used together with the scraper and belt conveyor to complete the outward transportation of coal. The structure of the transfer machine is relatively simple, and its main components are: guide chute, motor, reducer, trolley, frame, chain scraper, chute, tail frame, etc.
Its basic working principle: the head part of the transfer machine is overlapped on the tail rail of the adjustable belt conveyor by the beam and the trolley; The tail part and the horizontal loading section are placed on the bottom plate of the chute, and it is necessary to ensure that the tail chute and the scraper are reliably overlapped; The transfer machine is driven by external forces (jack, winch, etc.) and moves with the continuous advancement of the working face. The effective maximum displacement is about the overlapping length of the transfer machine and the belt conveyor tail; The coal mined by the shearer is transported to the transfer machine by the scraper, and then to the belt conveyor by the transfer machine to realize the outward transportation of coal and form the continuous transportation operation of coal flow.
2 Fault analysis and treatment measures of the transfer machine
2.1 The motor cannot be started
Cause analysis: excessive load; The motor wiring is not reliable and there is phase loss; Control circuit fault, etc.
Solution: reduce the load and unload part of the coal on the equipment; Check the circuit, find the defects and damaged parts, repair or replace the circuit; Check whether there is phase loss and whether the current of each phase line of three-phase power supply is balanced. 2.2 Chute wear
Cause analysis: chute wear is a common failure of all chute types as conveying channels. The main causes of chute wear are material wear and bite wear. Material wear refers to the relative displacement between the coal transported by the transfer machine and the surface of the chute, resulting in friction and wear on the surface of the chute. The bite wear refers to the plastic deformation when the surface pressure of the chute exceeds the yield strength of the chute material, and the chute material is damaged by wear.
Solution: The chute shall be made of materials with good wear resistance; Add wear-resistant coating and wear-resistant lining on the inner surface of the chute.
2.3 Drive chain failure
Manifestation: chain fracture and chain wear.
Cause analysis: The main cause of chain fracture is that the load of the transfer machine is too large, a large number of grinding stones are poured into the transfer machine, which causes the chain to break or wear seriously, and the chain has not been replaced in time. The chain and the chute have been friction for a long time, which causes partial damage to the chain, the bearing capacity is reduced, and the chain fracture occurs. The main causes of chain wear are improper maintenance, chain over-run, etc.
Countermeasures: do a good job in chain maintenance, prevent long-term friction between chain and chute, and do a good job in lubrication; Replace the damaged chain part; Overload operation of the transfer machine is prohibited; Replace the chain running beyond the time limit.
2.4 Shaft guard plate wear protection
The shaft plate is a vulnerable part. The defective operation of the shaft guard plate will cause the failure of the head bearing sprocket, and also cause the bottom coal pulling of the transfer machine.
Cause analysis: the drive chain and scraper caused impact and friction on the shaft guard at the machine head.
Solution: First, ensure that the material of the shaft guard plate is qualified and the installation and use meet the requirements; Secondly, do a good job of daily patrol inspection.
2.5 Scraper fault analysis
Cause analysis: the floor of the mine transportation roadway is uneven, the transfer machine and the floor of the roadway are in poor contact, and excessive load acts on the transfer machine during the working process, causing the connection between the tanks to break; The bolts are not firmly fixed, which makes the scraper and the press plate separate, causing jamming, and the chain wheel is not flexible; Overload operation causes fatigue wear and even fracture of the scraper; During the coal mining operation, the roof falls or the structural belt is broken, and the large grinding stone is hit on the scraper of the transfer machine with the scraper, which causes excessive stress and bad deformation or even fracture.
Solution: Before the operation of the transfer machine, it should be in good contact with the roadway floor, and the cushion measures can be taken; Do a good job of spot check and tighten loose bolts in time; During coal production, overload operation of the transfer machine is strictly prohibited; Preventive measures shall be taken when the roof is weak and passes through the structural zone.
2.6 Sprocket failure
Usually the sprocket failure occurs in the head and tail sprocket.
Cause analysis: the seal of the sprocket failed, resulting in oil leakage, causing the sprocket to work at high temperature; The overload operation of the transfer machine causes cracks and pitting on the surface of the sprocket, and the scope of pitting is expanded, resulting in fatigue fracture of the sprocket.
Solution: do a good job of spot inspection; Control the operating load of the transfer machine to avoid overload operation.
2.7 Reducer operation failure
During the operation of the transfer machine, sometimes the reducer makes abnormal noise and the vibration increases.
Cause analysis: poor gear engagement, broken teeth, serious gear wear, and foreign matters in the reducer; The coupling between the motor and the reducer is misaligned, the coupling gear sleeve is seriously worn, the gap is too large, and the coupling fastening bolts are loose.
Solution: the reducer should be checked regularly; The oil shall meet the requirements; The coupling installation must be aligned, and the straightness meets the requirements; If the coupling gear sleeve is worn, replace it in time; Do a good job of spot inspection and ensure that the bolts are fastened reliably.
2.8 Hydraulic coupling slipping
Cause analysis: insufficient liquid volume or leakage in the coupling device; Overload operation of the transfer machine; The chain is stuck, etc.
Solution: replenish liquid volume; Repair the sealing of the leaking part; Reduce the load of the transfer machine (unload part of the coal); Dredge the jammed part of the chain.
3 Summary
Bridge loader is the main intermediate transport equipment in fully mechanized mining face. It is one of the main equipment for modern coal mining. Due to the poor working conditions of the coal mining and conveying system, the probability of the failure of the transfer machine increases. In the use work, it is necessary to analyze all kinds of faults, summarize experience, and do a good job in maintenance, so as to effectively reduce the occurrence rate of all kinds of faults, improve the troubleshooting and solving ability, so as to improve the effective utilization rate of the transfer machine and realize the safe and efficient production of coal mining enterprises.